SIDEL SBO 18, KHS Monobloc Isobarometric Filler (1999)
219,000 € (ExWorks)
Get an official quote
Fill in the information below to receive an official quote on the machine you have selected.
Country:
France
Year:
1999
Category:
Filling
Manufacturer:
SIDEL
Model:
SBO 18, KHS Monobloc
Availability:
Immediately
SKU:
FR-FIL-SID-1999-00001
Overview
This SIDEL blow moulder and KHS filling monobloc were both manufactured in 1999. They are still in production until the end of October and can be viewed in person. The special feature of the filler is that it can process carbonated or still mineral water with natural flavors using a micro-dosing unit.
The filler (KHS Innofill monobloc) and accumulation table (Sidel AQ) are also available without the blow molder (Sidel SBO 18 Series 2), price on request.
Technical Details
Blow moulder | SIDEL | SBO 18 Series 2 | 1999
- Current capacity: 23.400 bph in 1.25L
- Working hours: 40.000
- Number of moulds: 18
- Moulds type: Shell type quick change
- Formats produced: 1.25L
- Bottles: Cylindrical petaloid base
- Oven type: Sidel
- Neck personalization: PCO 1881
- Type of preforms: with recycled PET resin
- Machine was regularly maintained
- Machine equipped with:
- Sidel preform tipper
- Sidel hopper with cover & feeder
- Sidel preforms unscrambler
- Sidel preforms infeed rail
- Blowing station for 18 moulds
- Sidel electrical cabinet with Siemens
- Sidel PCC drive & control
- Lanfranchi bottles buffer storage silo
- Unscrambler and air conveyor system with drive to the entry KHS monobloc
- Supplied with all format & spare parts available
Rinser, Isobarometric Filler, Capper Monobloc | KHS, Zalkin | VK-E 40/50/10/S PET | 1999 (low working hours)
- Filling carbonated mineral water and also carbonated mineral water with natural flavours
- Processing: PET bottles 1,25L & 0.50L cylindrical petaloid base
- Bottle neck: PCO28 1881
- Current capacity: 23.400 bph
- Number of rinsing nozzles (KHS Innoclean): 40
- Number of filling valves (KHS Innofill): 50
- Number of capping stations (Zalkin): 16
- Including also micro-dosing unit Perrier for natural flavours
- With caps magazine & elevator
Accumulation table Gebo Sidel type AQ file
- Dynamic accumulation and buffer between the filler outlet and the labeller inlet, avoids untimely stops upstream (filler, blow-moulder) due to the labeller
*There may be differences between the data shown and the actual values, this should be confirmed by the sales representative.
If you have any further questions please contact us
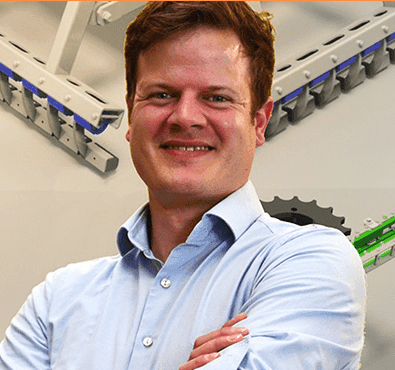
Carsten Hormes
Your Account Manager
CLICK TO CHAT ON WHATSAPP
Related Products
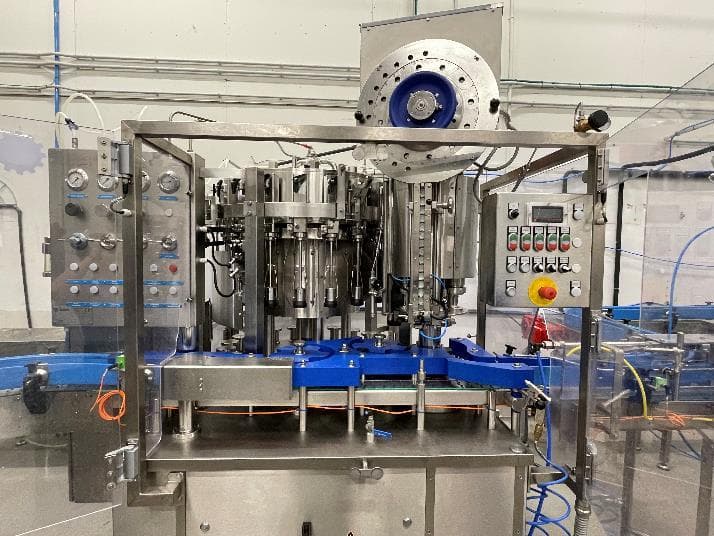
Markl - 2021 - Spain
Isobarometric Filler
190,000 €
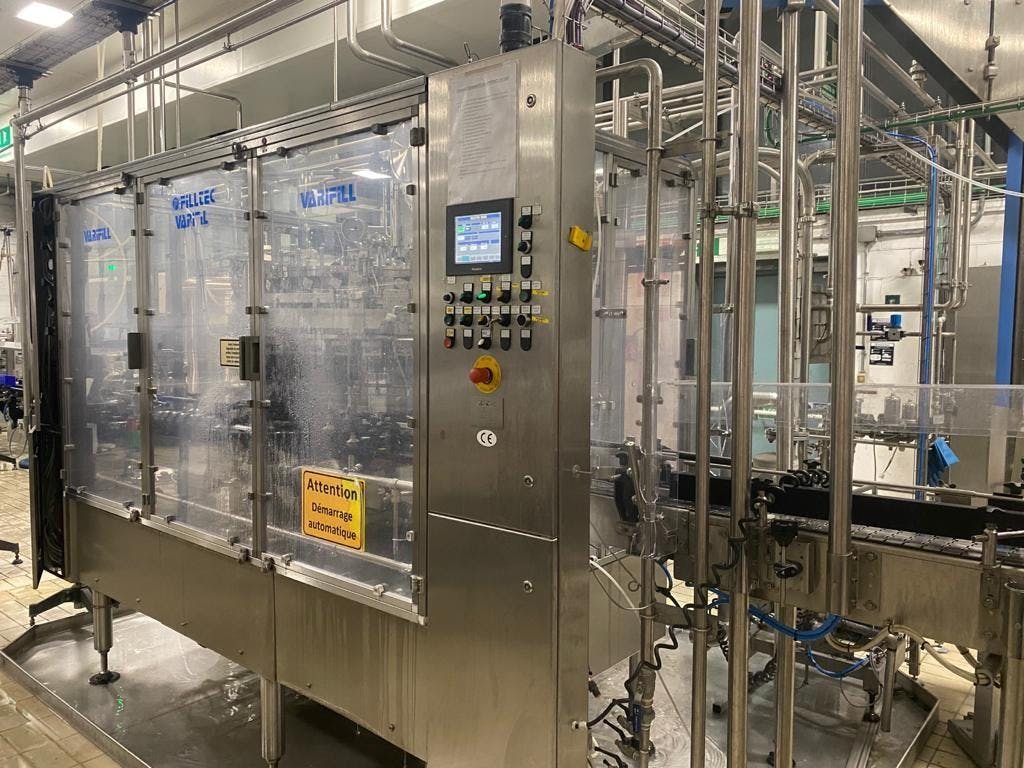
Filltec - 2006 - Italy
Isobarometric Filler
60,000 €
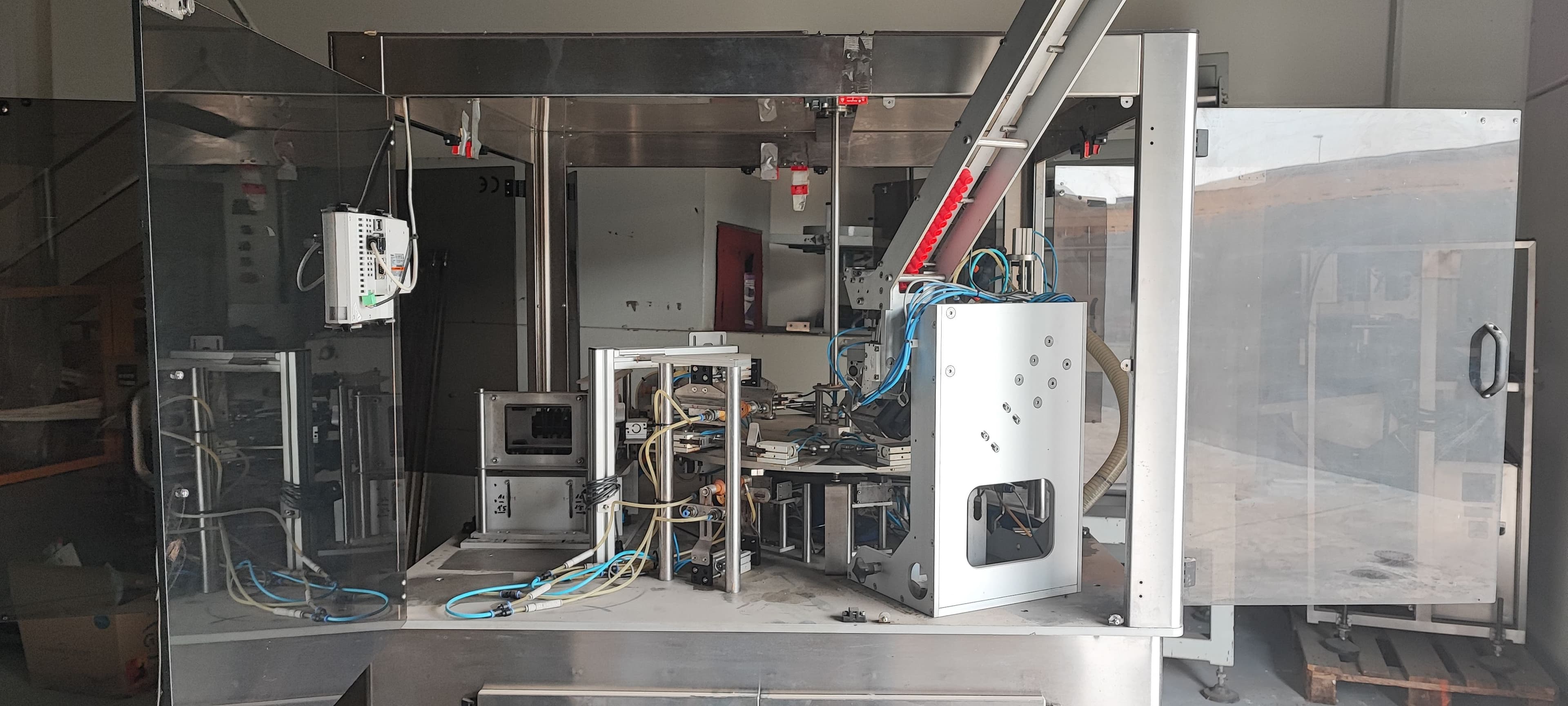
AIT - 2010 - Spain
Bag Filler
69,000 €
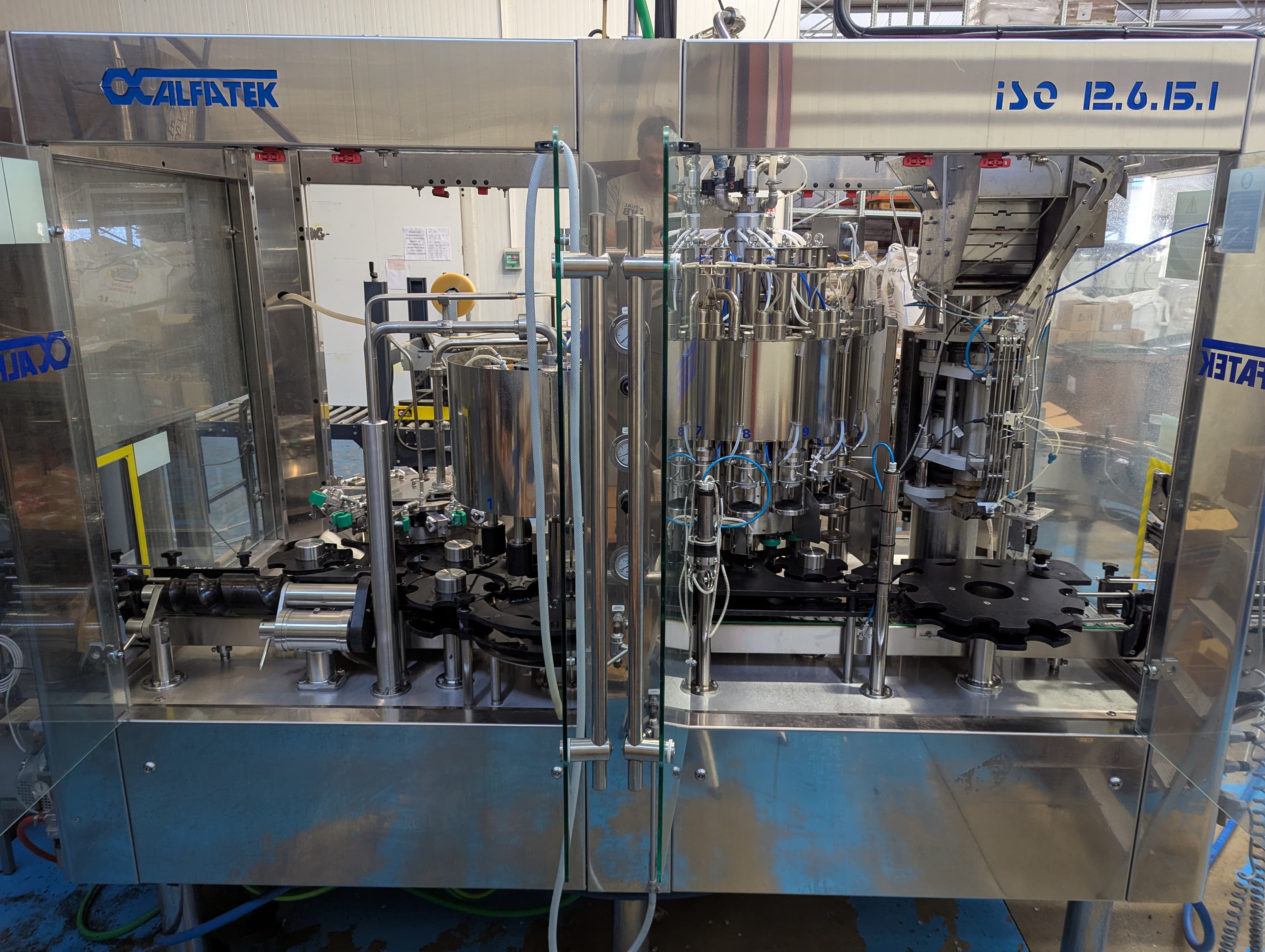
Alfatek - 2012 - France
Isobarometric Filler
40,000 €
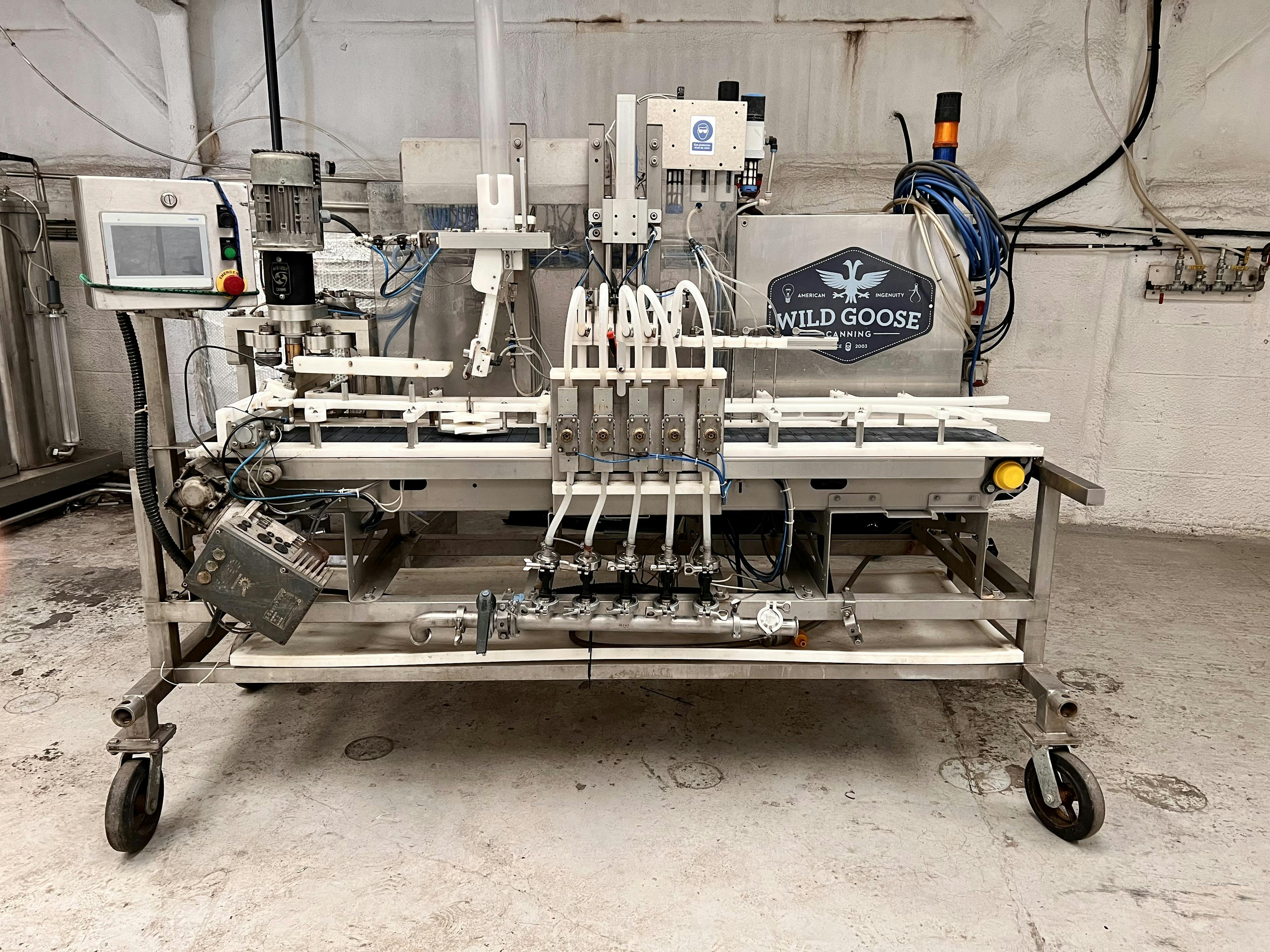
Wild Goose - 2018 - United Kingdom
Atmospheric filler
58,000 €
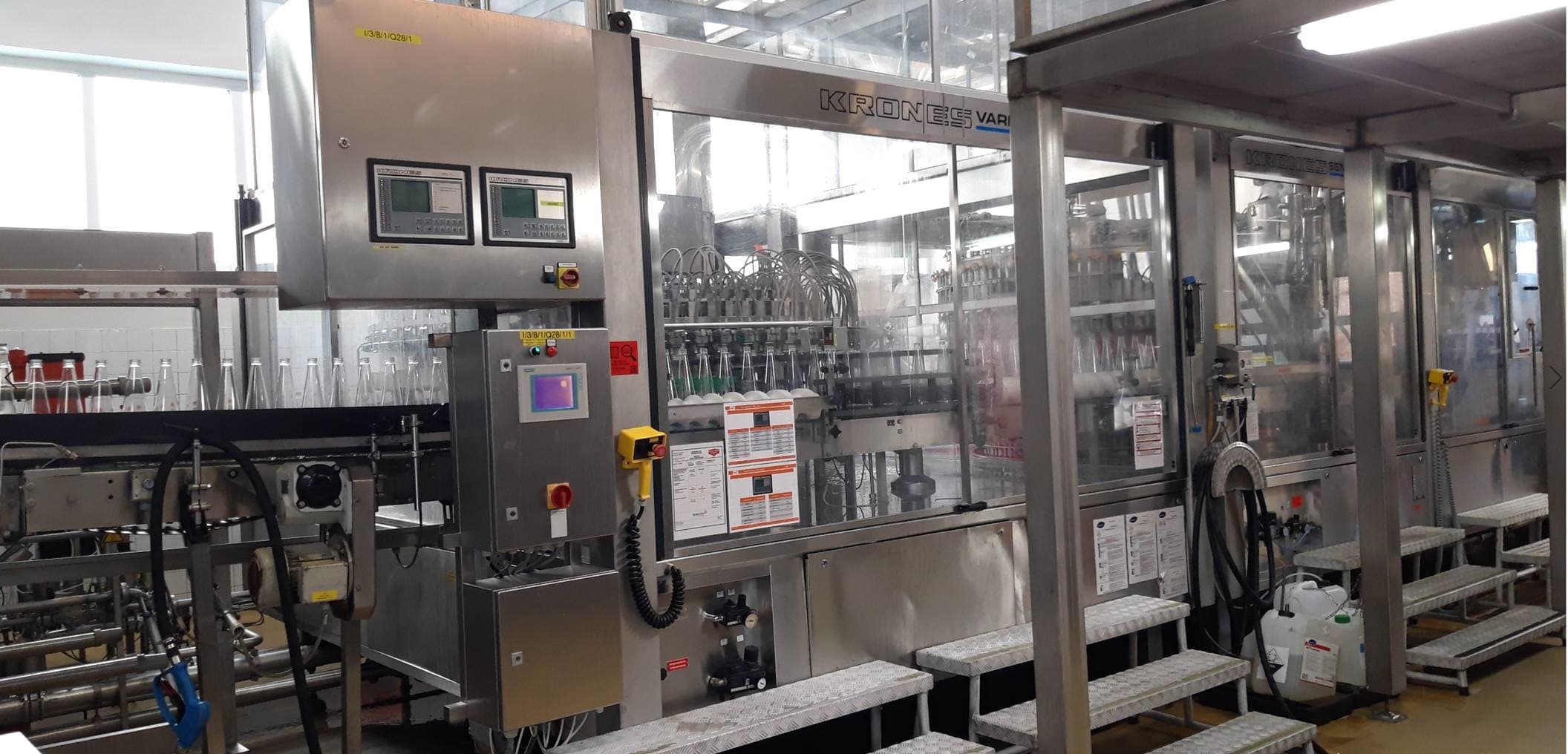
Krones - Sensometic - 1999 - Germany
Vacuum Filler
82,000 €
Vipoll - 2013 - Germany
Isobarometric Filler
97,500 €
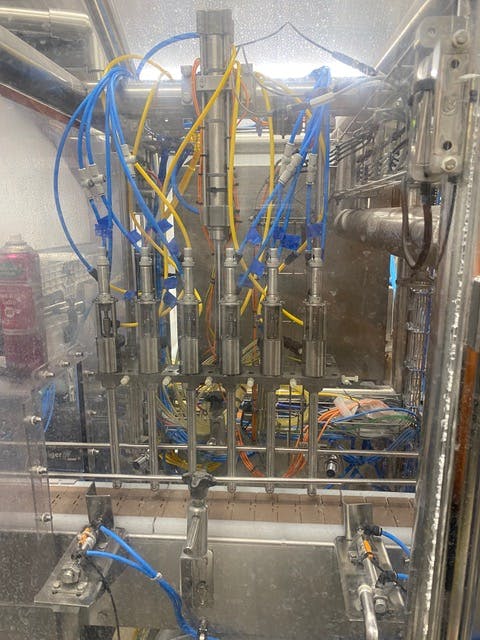
Innovus - 2019 - United Kingdom
Atmospheric filler
26,500 €
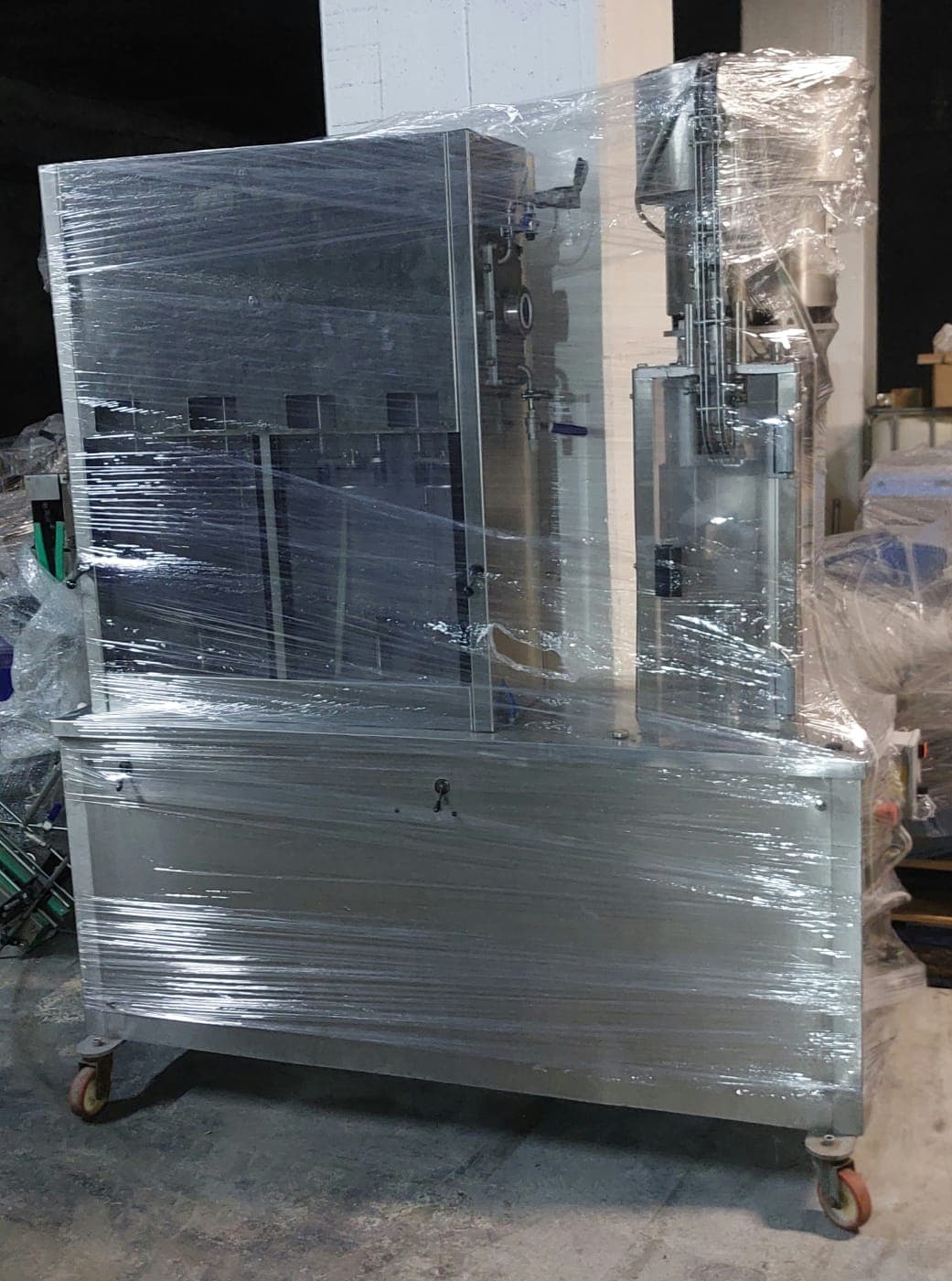
Barida - 2015 - Spain
Isobarometric Filler
16,000 €
TetraPak/ AlfaLaval - 2014 - Switzerland
Filling Line
370,000 €
MBF - 2004 - Austria
Vacuum Filler
25,000 €
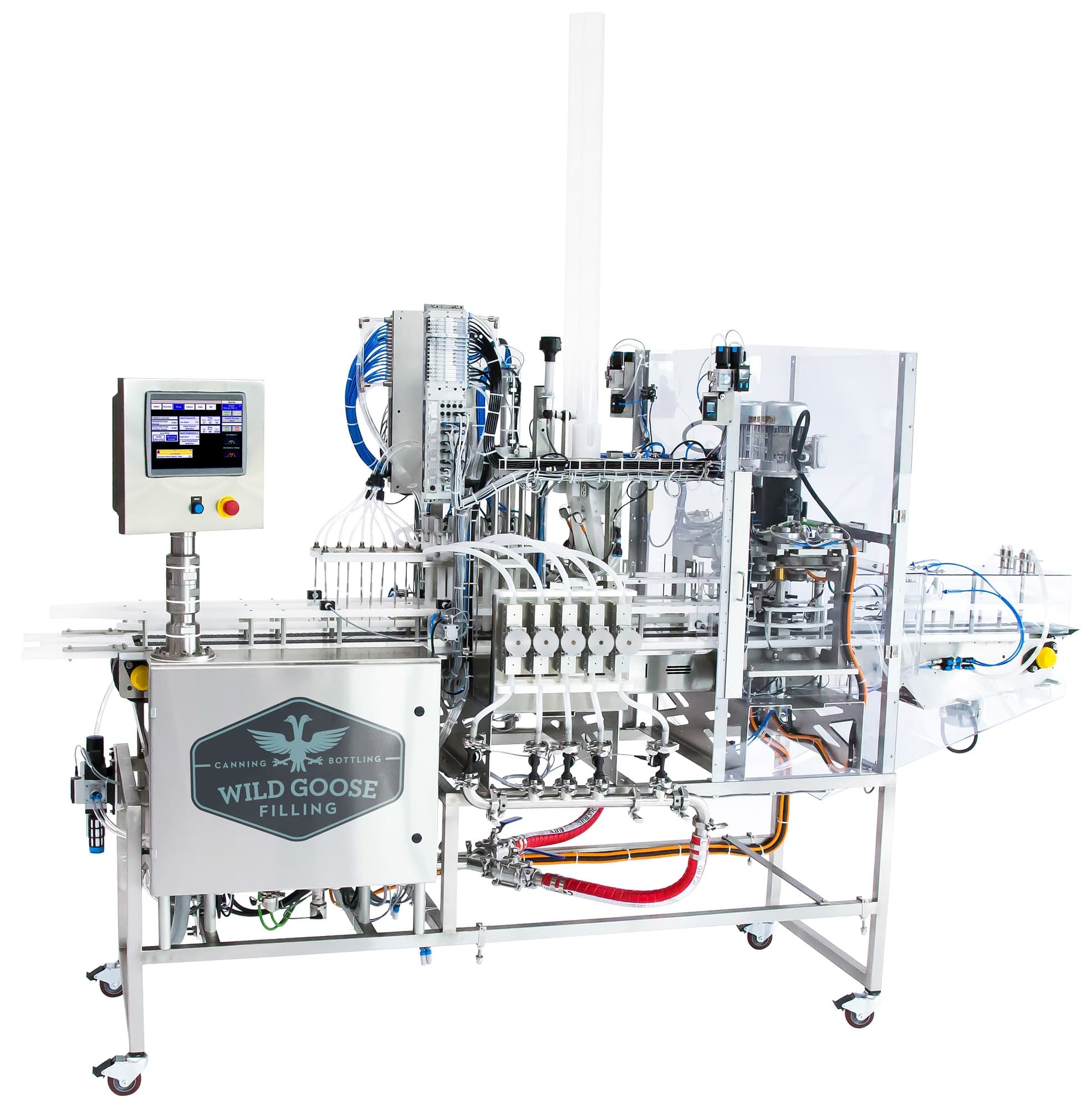
Wild Goose - 2023 - Spain
Atmospheric filler
193,400 €
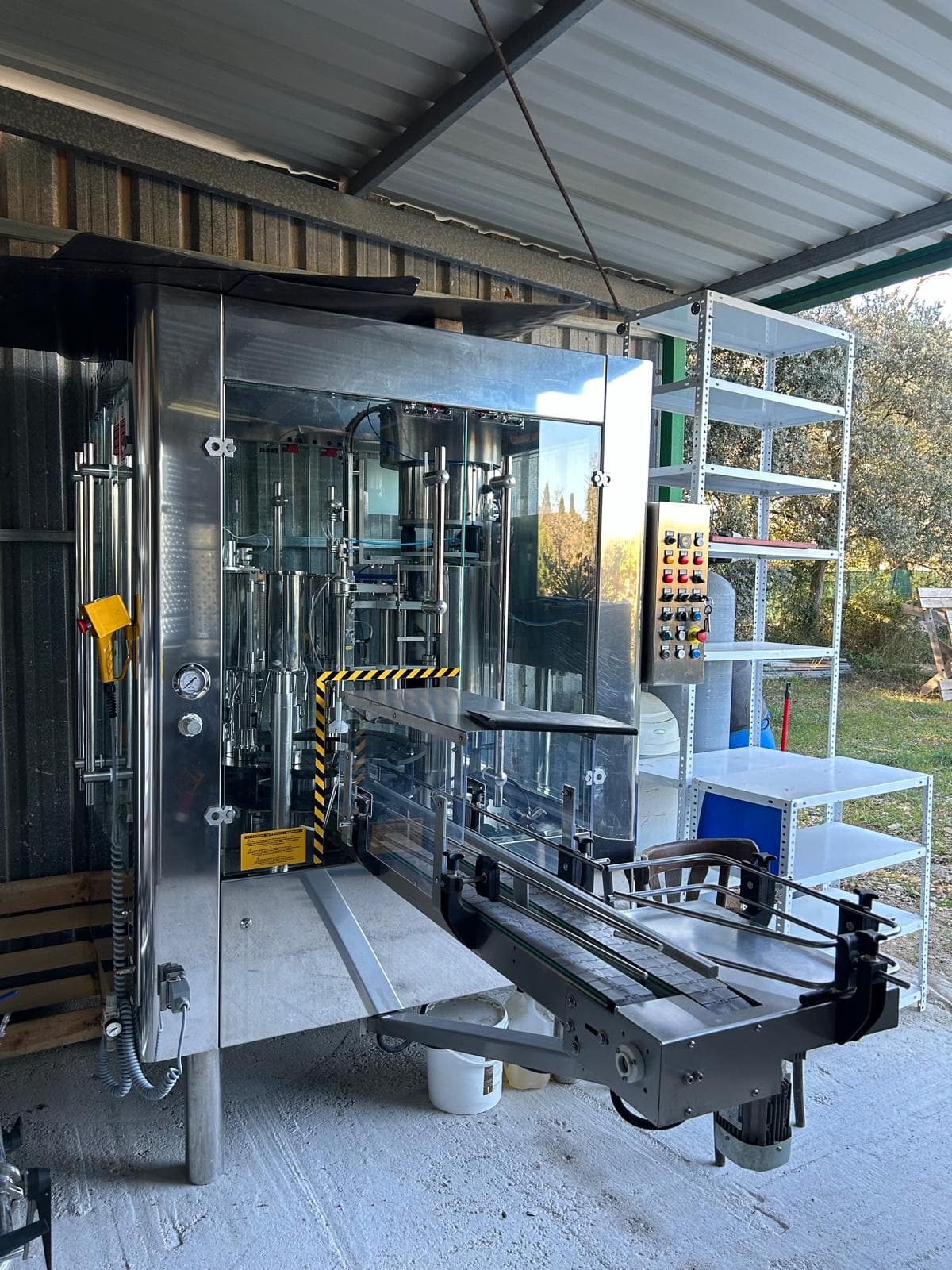
Alfatek - 2018 - Spain
Atmospheric filler
19,500 €
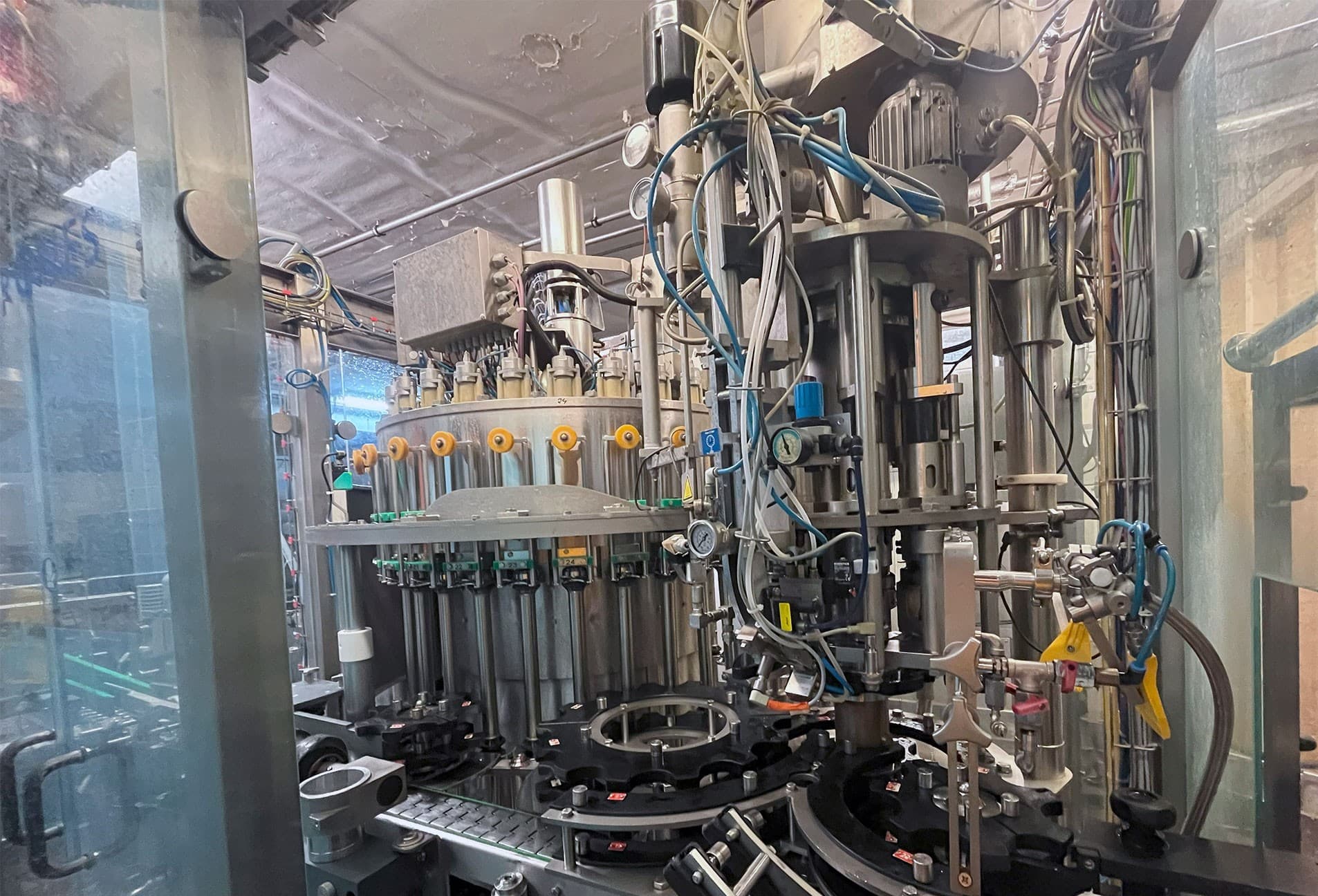
KOSME - 2011 - Germany
Isobarometric Filler
165,000 €
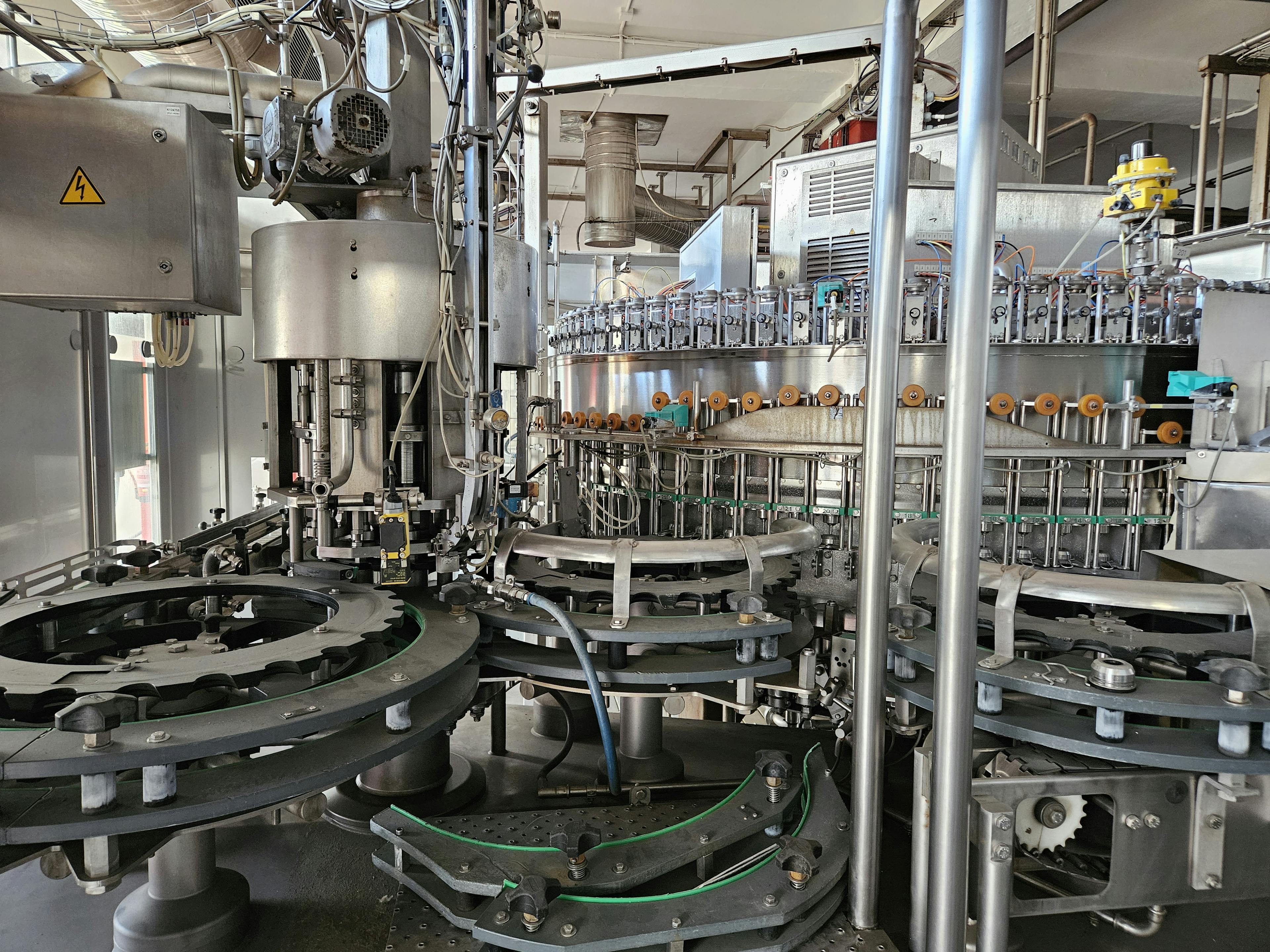
Krones - 2007 - Spain
Isobarometric Filler
60,000 €
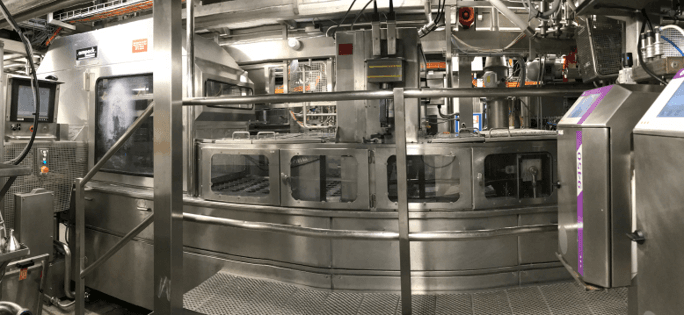
Ampack Amann - 1997 - Germany
Cup filler
60,000 €
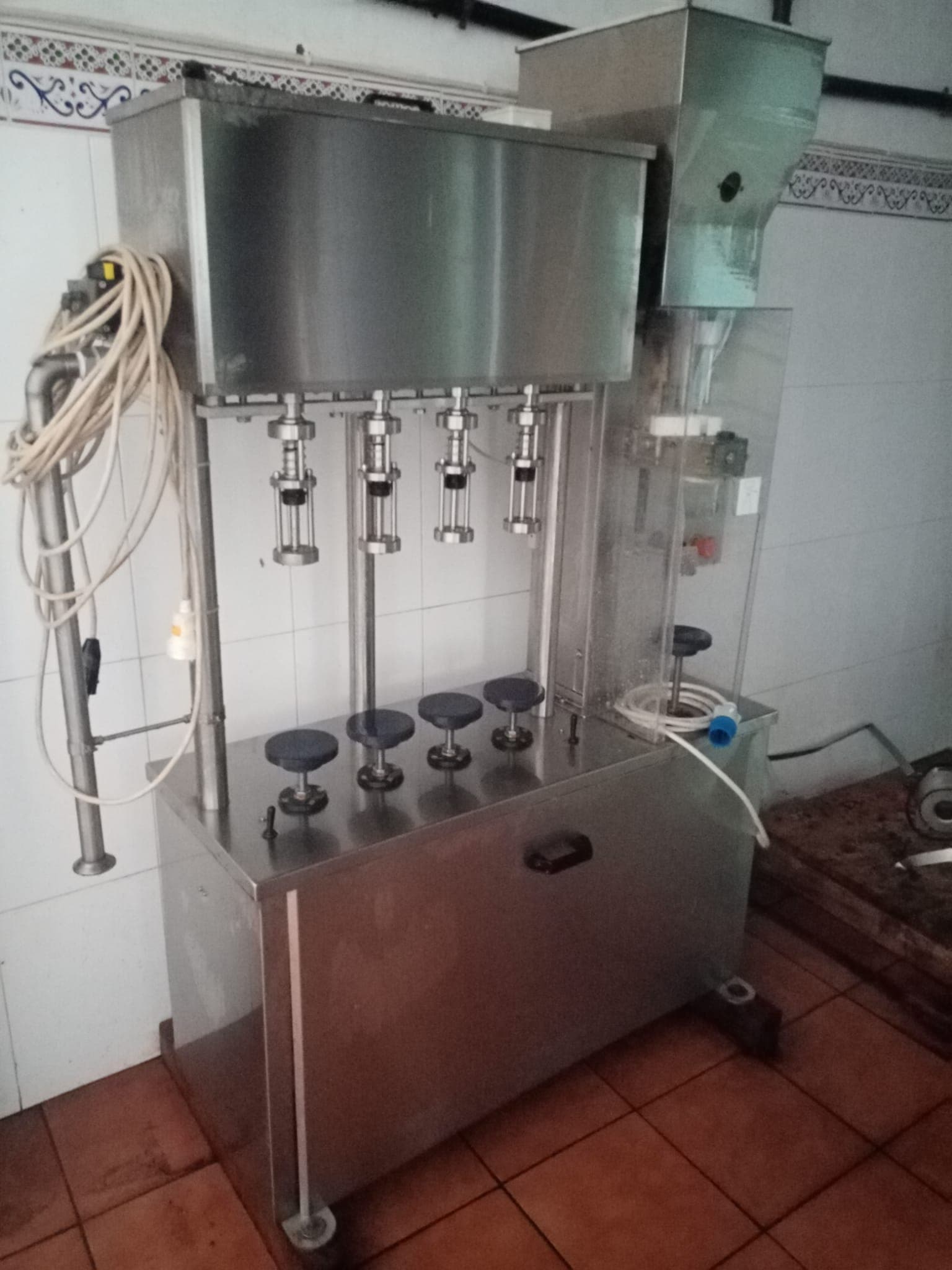
Officine Pesce - 2005 - Spain
Atmospheric filler
12,000 €
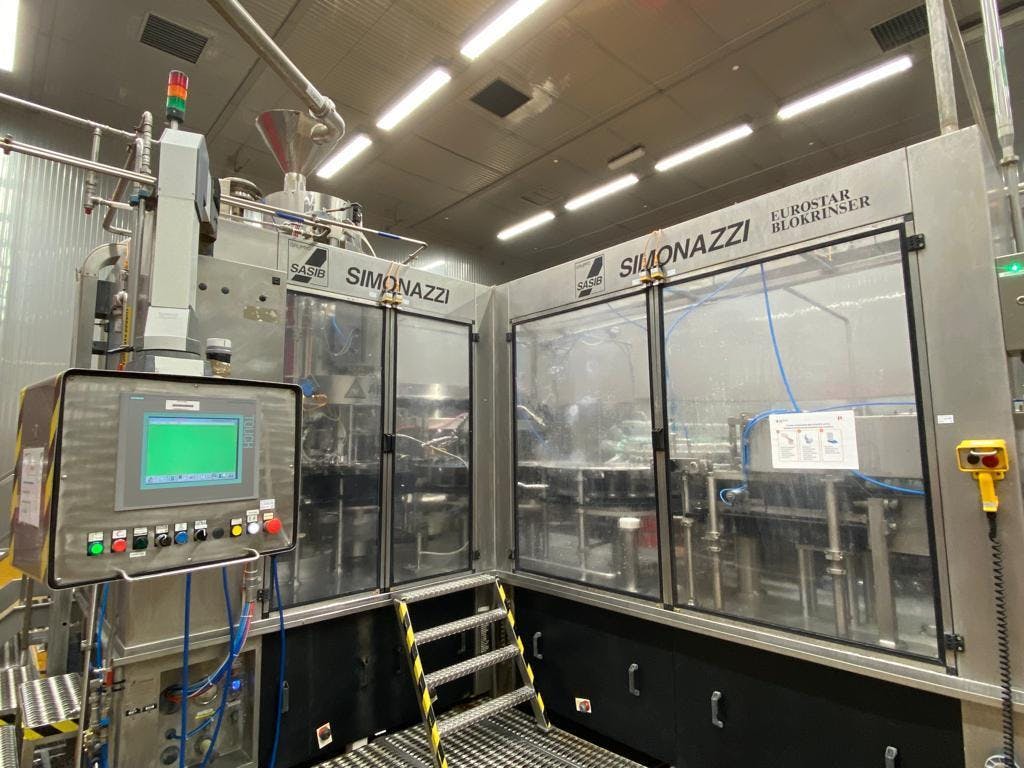
Sasib/ Simonazzi - 1993 - Italy
Isobarometric Filler
90,000 €
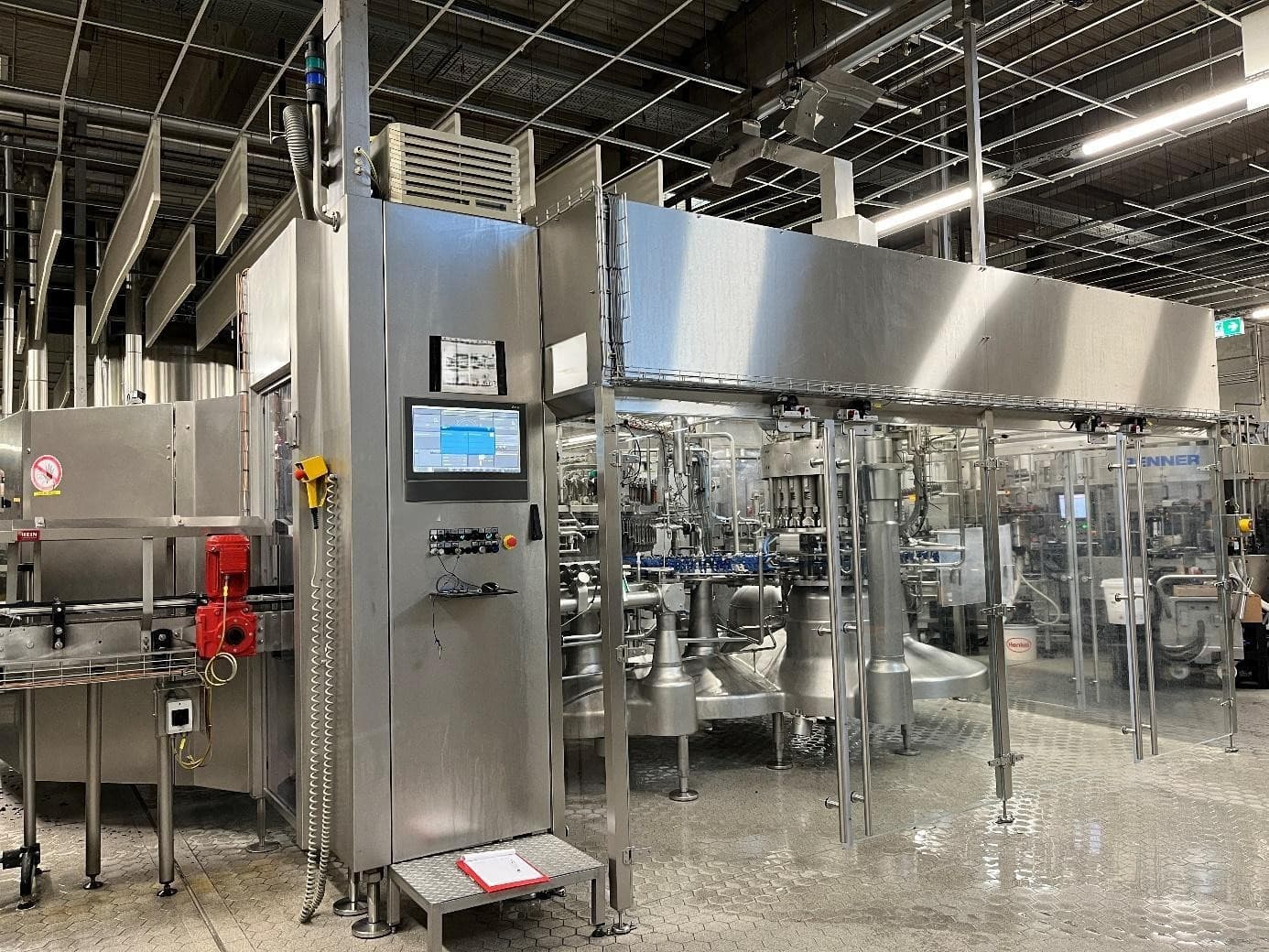
KHS - 2002 - Germany
Isobarometric Filler
195,000 €
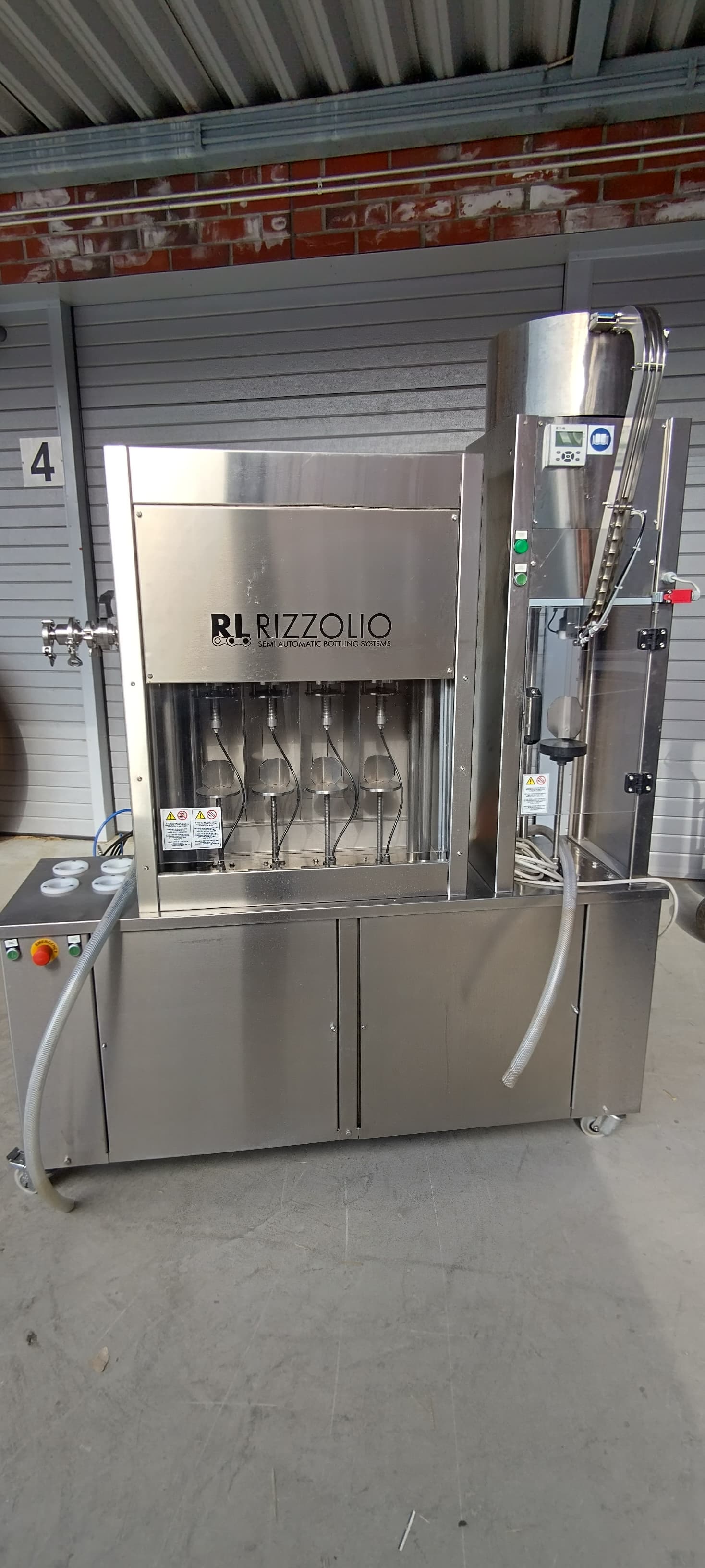
RL RIZZOLIO - 2016 - Finland
Isobarometric Filler
19,000 €
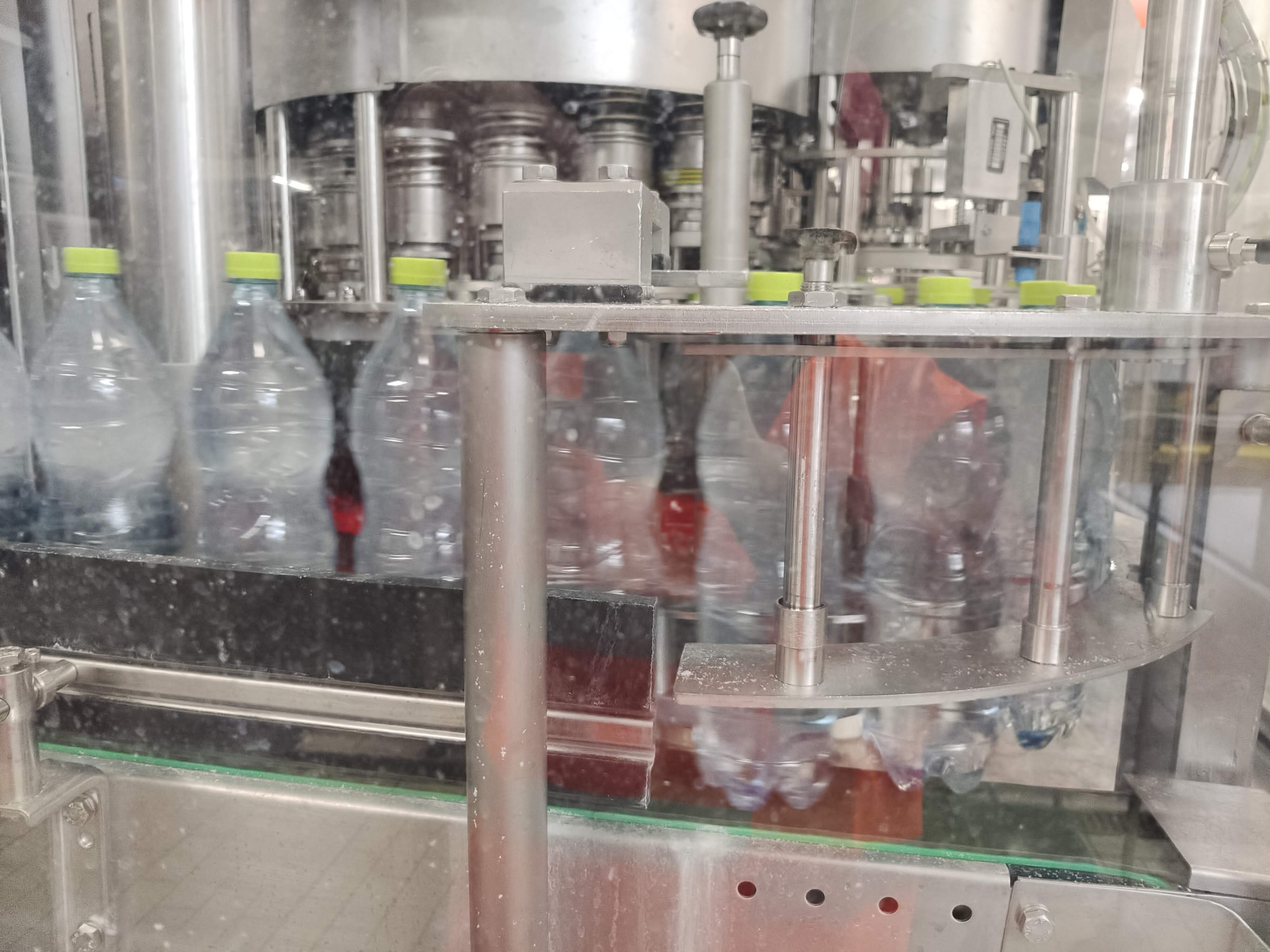
KHS - 1999 - France
Isobarometric Filler
118,000 €
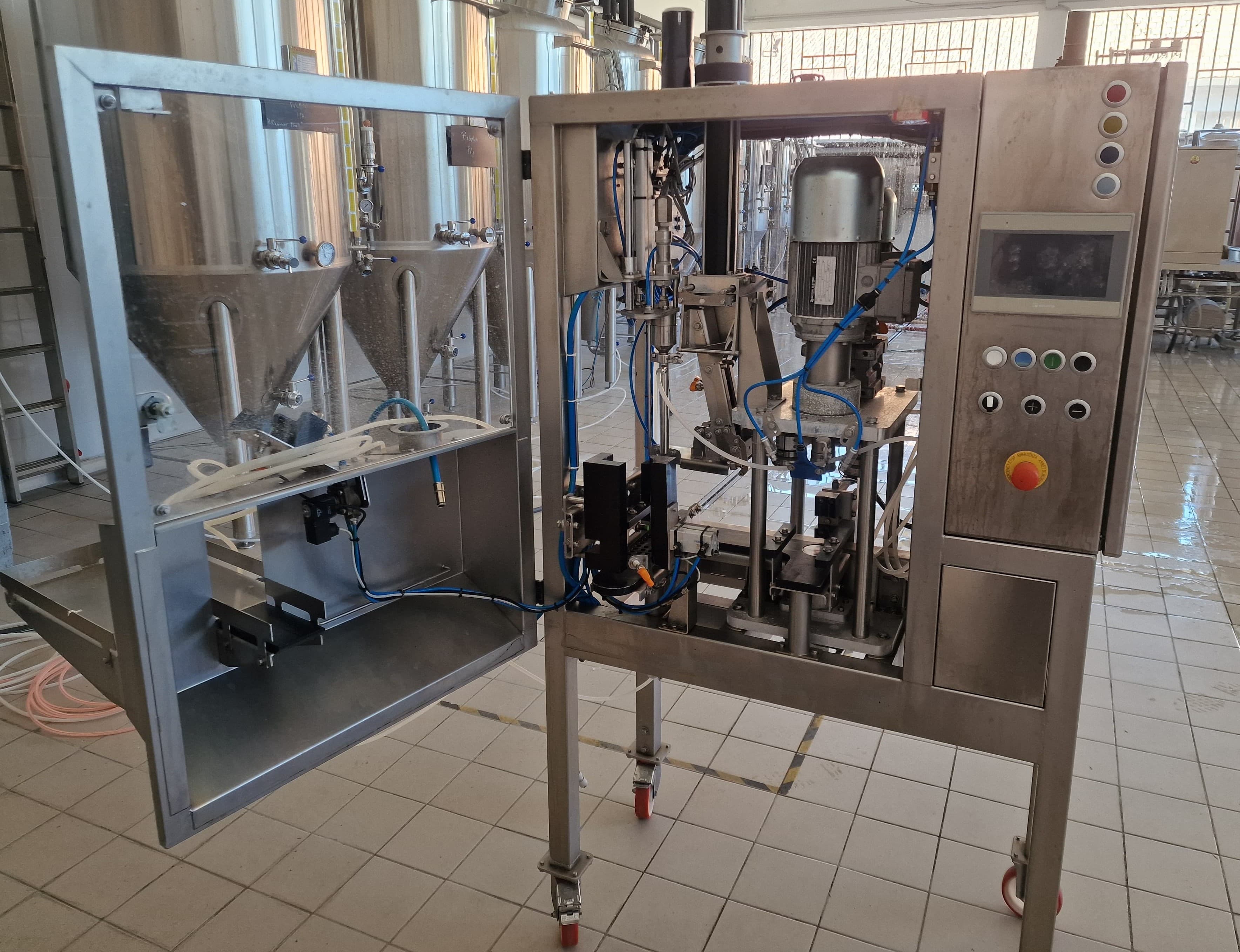
EMMA - 2020 - Spain
Isobarometric Filler
32,000 €
KHS - 2013 - Germany
Isobarometric Filler
250,000 €
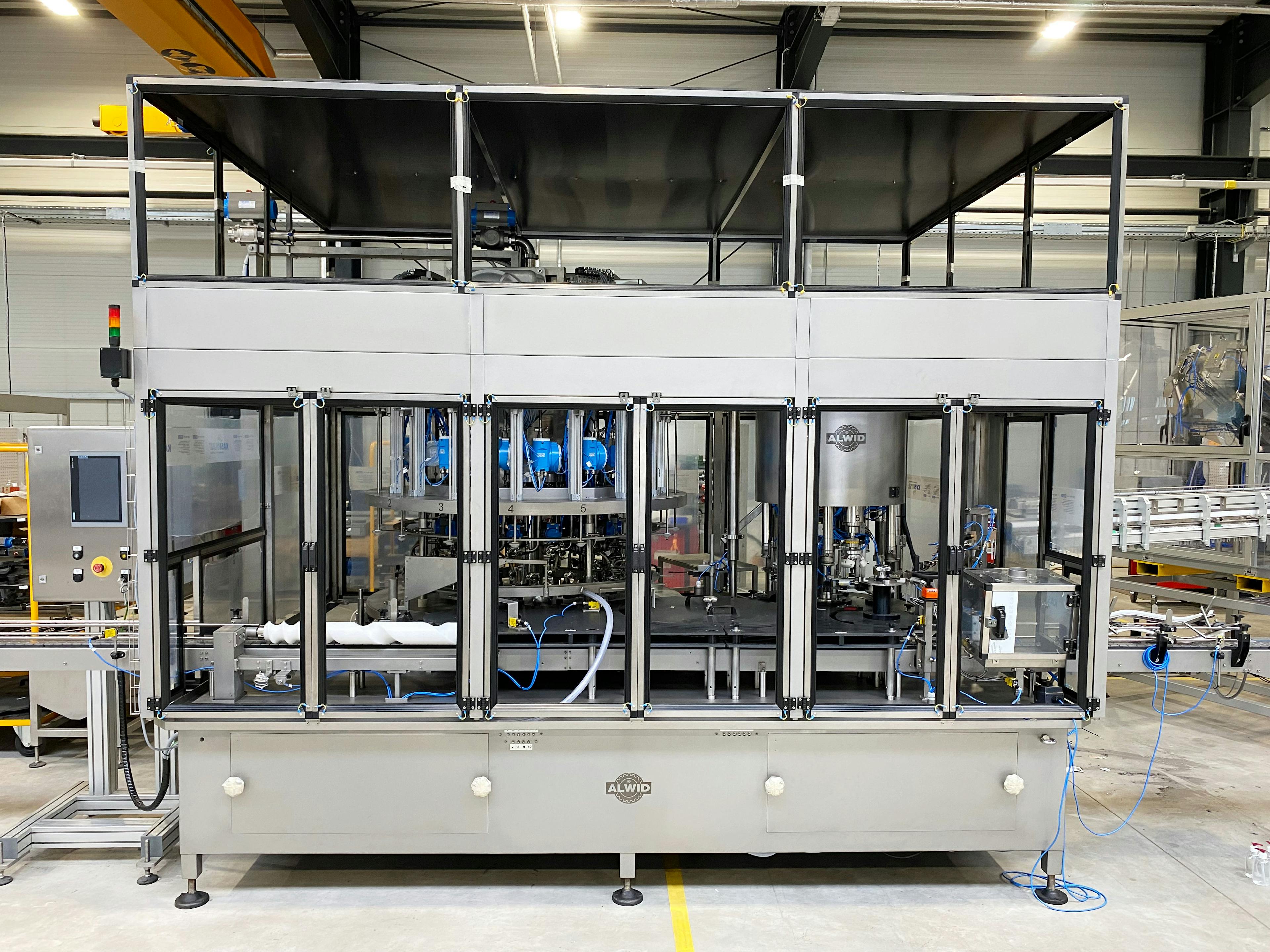
ALWID - 2021 - Germany
Vacuum Filler
705,889 €
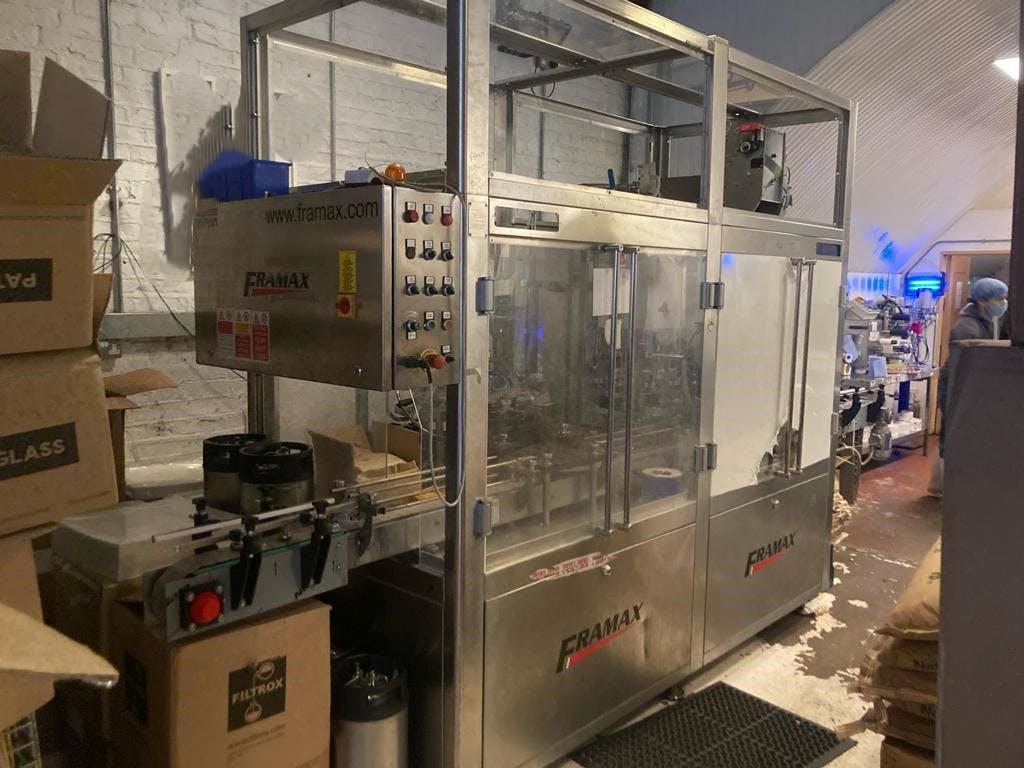
Framax - 2012 - United Kingdom
Atmospheric filler
29,700 €